E Nand Gopal, Manager – Clean Energy, PwC India
Nilesh N. Shedge, Energy Tech. Director, Enerlly.com
The industrial sector plays a pivotal role in the overall economic development, employment creation and effective reduction in poverty of the country. Zimbabwe’s manufacturing sector contributes nearly 10% to the country’s GDP. The prevailing power deficit leads to unmet demand/load shedding in end-use sectors including industries. Industries, competing in the global markets, need to be watchful of both, production costs as well as environmental impact of their activities. The rising energy costs and increasing awareness of adverse environmental impact has brought energy efficiency to the forefront.
The rationale for energy efficiency (EE) in the country are three-fold. Firstly, the vintage of technology in manufacturing sector requires innovative approaches to energy conservation. Energy technology is changing so rapidly that state-of-the-art techniques have a half-life of ten years at the most. Secondly, the economy is on a track of recovery, which implies the capacity utilization of the industries are gradually increasing, thus moving for energy efficient options can help improve the product yield. Thirdly, a reduction in energy costs to manufacture the product can be immediate and permanent, thus enhancing profit margins of industries.
Based on experiences of travelling across the country and conducting energy audits of multiple industries, in Zimbabwe, industries are typically reluctant to invest in energy monitoring. For instance, Panasonic factory in Japan has 6000 monitoring points (learning from a site visit, 2013). Similar size factory in Zimbabwe would fail to reach 100 monitoring points. The most recent advance in EE in industry is monitoring of process parameters based on Internet of Things (IoT) and analysis of behavior/pattern of data using machine learning to provide precise control and run factories efficiently.
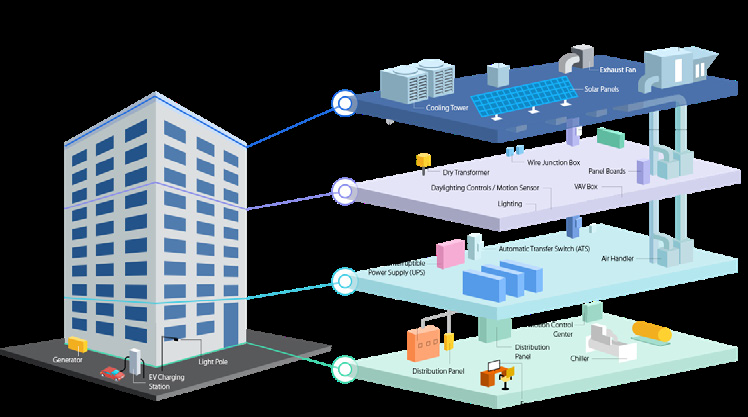
A close and real-time monitoring of energy flow data is thus a necessity for reducing energy costs and increasing environmental friendliness. Industries (and commercial facilities) usually depend on the monthly electricity bill to assess the energy performance of their plant, but a monthly energy bill can only provide a broad picture, which isn’t enough to analyze the energy distribution down to applications and doesn’t provide actionable information. For insights and proper analysis, the real-time energy and power data is of utmost importance. A typical cycle of energy efficiency improvement is presented in the figure.
A typical energy management system uses energy meters, air / water / steam flow meters to measure the data. Recorded data is transferred to a system and engineers spend days analyzing the data to draw patterns and arrive at meaningful trends (which is a tedious process and is not religiously followed by industry). Based on these trends, energy losses are quantified. A plan of action is drafted to either reduce, reuse or optimize the energy consumption. The verification is done by recording the data post implementation of EE measure. There is a lot of human involvement in the process and it is prone to errors. Since the manual activities are not real-time, many opportunities to take immediate action are lost. As a result, the inefficiencies get aggravated over a period of time leading to excess production costs.
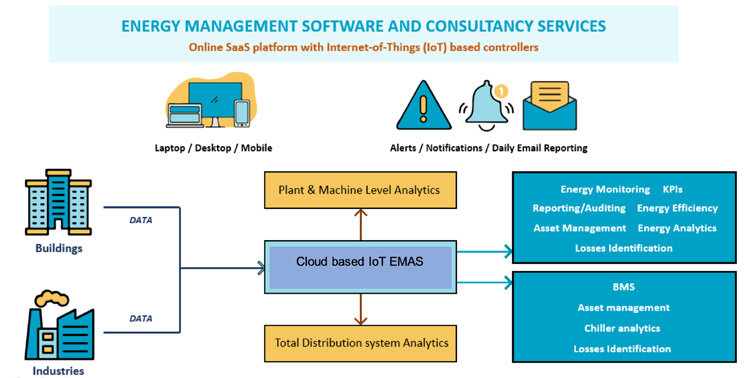
In an IoT based energy management system, all the tasks in the Cycle of Energy Efficiency, except “Optimization” i.e. taking action to reduce the losses is automated and done by an IoT tool, thus minimizing human errors. The IoT tool assists in making an informed decision by providing insights into energy performance indicators of total plant, sub-process, machine level and to identify losses in systems. The IoT system then uses data analytics-based machine learning to predict and capture the losses in the system such as over/under loading, idle running, leakages etc. The IoT system can be tailored based on the needs of the industry, providing hourly/daily/weekly energy performance reports and send alert notifications through WhatsApp, Email or alarm in case the energy performance indicators vary beyond pre-set thresholds. A systematic view of an IoT based energy management and analytics tool is presented in the figure.
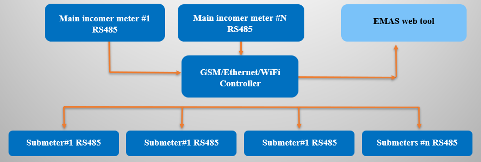
An Internet of Things (IoT) based Energy Analytics and Monitoring system comes with a hardware controller and Software-as-a-Service (SaaS) online platform, that assists industries to gain competitive advantage by gaining energy efficiency and compliance. The IoT controller collects the data in real-time through RS485 based energy meters and transmits it to cloud platform, where it is analyzed and displayed on the online secured portal (see figure for IoT EMAS setup).
The online secured portal can be accessed using right credentials (login/password) through any digital devise having Internet connectivity. Under the hood, IoT operates complex algorithms that analyze parameters against different international standards such as ISO 50001:2018 Energy Management System. An IoT EMAS can offer following features.
- Real time monitoring parameters like Voltage, Current, PF, kVA, kVAh, kW, kWh, Hz and power quality parameters harmonics, unbalances.
- Mapping of Analytical parameters like Specific Energy consumption (kWh per unit production), Specific Energy Cost and Specific GHG Emission
- Easy access to historical data (measured/analytical data) which can be downloaded from the portal
- Automated Benchmarking, Target setting which enables to adopt LEAN manufacturing techniques such as KAIZEN/5S
- Losses identification in equipment such as Transformers, Air compressors, Pumps etc.
- Asset management for Solar Photovoltaics, Diesel Generator set, etc.
- New features with more analytical capabilities can be added frequently as a software update, making it more advanced
- Set and receive alert and notifications for parameters for taking remedial action
- Daily Automated Email reporting
- Easy integration of communication-based flow meters/gas meters/BTU meters for HVAC and other systems

The tool can assist industry build a roadmap for energy efficiency based on the feedback received from analytics software. Successful case studies have proven energy savings results of up to 10% in industry and the payback period is under one year. IoT based EMAS can help industry reduce energy cost, enhance profitability and assist Zimbabwe achieve its GHG reduction targets.
Disclaimer: The views in the article are of authors and do not reflect the views of firms associated.